Marine semi-welded plate heat exchangers
Semi-welded plate heat exchangers are suitable for fuel conditioning duties involving alternative fuels, LPG cargo handling duties, refrigeration duties and Organic Rankine Cycle (ORC) duties. Our marine line features the unique Alfa Laval RefTight™ sealing system, which guarantees a long lifetime sealing between the welded channels because the laser weld is on the outside of the ring gasket groove. The smooth surface ensures a tight uniform seal over the entire gasket ring.
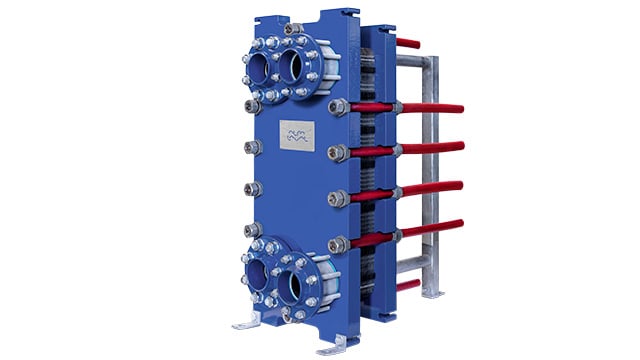
Highly efficient and flexible marine heat exchangers
- High efficiency that reduces energy consumption and OPEX
- Long service life, comparable to the vessel lifetime
- Serviceable without hot work, protecting uptime
- Easy maintenance on board through CIP or mechanical cleaning
- Extendable capacity through the addition of plates
Alfa Laval’s marine semi-welded plate heat exchangers are available for a broad range of temperatures and media, with operating pressures up to 65 bar. Robustly constructed, they provide exceptional longevity with their resistance to vibrations and pressure cycles. The various sizes, which cover a wide spectrum of heat transfer capacities and flows, are carefully designed and selected to achieve optimal performance. The cooling media/seawater side is fully accessible without disconnecting the semi-welded plate heat exchanger from the pipework.
Documents
Downloads
Instructions and manuals
Product brochures
Product leaflet
Applications
Heating and cooling in the engine room
On a ship, there are many types of machinery with a cooling demand. When the heat energy cannot be recovered or utilized, the total costs of transferring it away from the machinery should be kept to a minimum. Alfa Laval can ensure a cost-effective central cooling system through our portfolio of innovative plate heat exchangers. Our gasketed plate heat exchangers have unique features that reduce the running costs for engine room cooling – and contribute to sustainability.
Heating and cooling for LPG cargo handling
The transport of LPG requires tailored cargo handling systems. Alfa Laval marine semi-welded plate heat exchangers are the ideal choice for the cargo condenser, thanks to their very high efficiency, their small footprint and the ease of performing service on board. The robust units resist vibrations and pressure fatigue, and more plates can be added if faster loading rates are desired.
Heating and cooling for methanol
As the marine industry decarbonizes, interest in methanol is growing and the first methanol-fuelled vessels are beginning to appear. Methanol is a clean-burning liquid fuel that enables carbon-neutral operations if produced from green sources. Yet it poses heating and cooling challenges compared to conventional fuels. Alfa Laval has the heat exchanger solutions to ensure safe and efficient work with methanol on board.
Marine refrigeration
Refrigerants are common in the marine industry, from chilling and freezing the catch on fishing vessels to air conditioning on cruise ships. Yet the refrigerant types are changing rapidly. Chlorofluorocarbon (CFC) and hydrochlorofluorocarbon(HCFC) refrigerants have given way to hydrofluorocarbon (HFC) refrigerants, and now many shipowners are exploring natural refrigerants like CO2. Alfa Laval has the heat exchanger solutions and expertise to support natural refrigerant choices.
Services
알파라발 마린 서비스
글로벌 네트워크를 통해 진행되는 알파라발 마린 서비스는 설비의 가동 시간을 늘리고 성능을 최적화를 지원하며, 장비의 수명 전반에 걸쳐 신뢰감과 효율성, 컴플라이언스를 제공합니다.
Higher pressures demand a higher standard
If your heating and cooling duties demand higher pressures, it’s time to demand a higher standard of technology. Discover total reliability and efficient thermal performance with the Alfa Laval marine line of semi-welded plate heat exchangers.
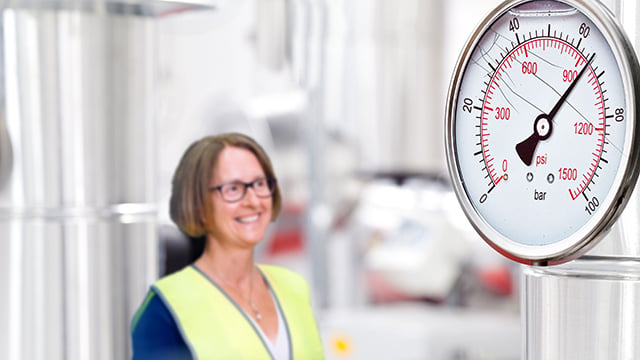
Highly efficient with unique sealing system
Alfa Laval marine semi-welded gasketed plate heat exchangers are suitable for liquids and gases incompatible with normal gaskets or at higher pressures. They are commonly used in refrigeration applications for evaporation and condensation.
The unique Alfa Laval RefTight™ sealing system guarantees a long life-time sealing between the welded channels because the laser weld is on the outside of the ring gasket groove. The smooth surface ensures a tight uniform seal over the entire gasket ring.
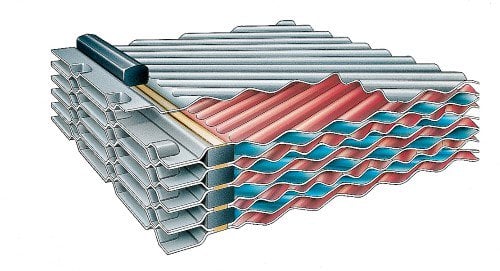
What make our plate heat exchangers so reliable, efficient and serviceable?
Equipped with well-designed features that make a difference, Alfa Laval marine semi-welded plate line of heat exchangers are easy to maintain and have a long service life.
RefTight™
sealing system
High performance gasket sealing for high-pressure duties
CurveFlow™
distribution area
Improves media flow and minimizes risk of fouling.
OmegaPort™
noncircular port holes
Enhances media flow and thermal efficiency.
ClipGrip™
gasket attachment
Ensures perfect seal and trouble-free maintenance.
Five-point alignment
Ensures reliable plate positioning and easy service of large units.
T-bar roller
Provides a lower unit that is easy to service.
How it works
The heat transfer area of a gasketed plate-and-frame heat exchanger consists of a series of corrugated plates, assembled between the frame and pressure plates, which retain the design pressure. For the highest thermal performance and to enable a very close temperature approach, fluids normally run counter-currently through the heat exchanger.
The sealing between the plates on the marine semi-welded line alternates between laser welds and gaskets. The laser welded channel allows use of fluids that are not compatible with normal gaskets and also allows for higher design pressure than fully gasketed plate-and-frame heat exchangers. Additionally, the Alfa Laval RefTight™ sealing system guarantees equal sealing force over the entire porthole gasket.
The marine semi-welded line is available with various pressing depths and angles of the chevron pattern and various shapes of the corrugation which are carefully designed and selected to achieve optimal performance. The CurveFlow™ and the chocolate pattern distribution area are two design features available that ensure fluids are evenly distributed across the entire plate. The result is that the entire heat transfer surface is fully utilized and stagnant zones that can result in fouling are avoided.
High flow turbulence between plates results in higher heat transfer; however, the consequence is pressure drop. Our thermal design engineers will help you design and select the model and configuration that is suitable for your application needs while delivering maximum thermal performance and minimizing pressure drop.

Liquid/Liquid GPHE
Steam Heater GPHE
>