Substantial water and energy savings revolutionizing the dairy industry
A small heat-exchanger accessory has recently made a significant impact at one of the largest dairy producers in Scandinavia by increasing uptime by 50% and, most importantly, reducing environmental impact through substantial water and energy savings.
DATE 2024-09-17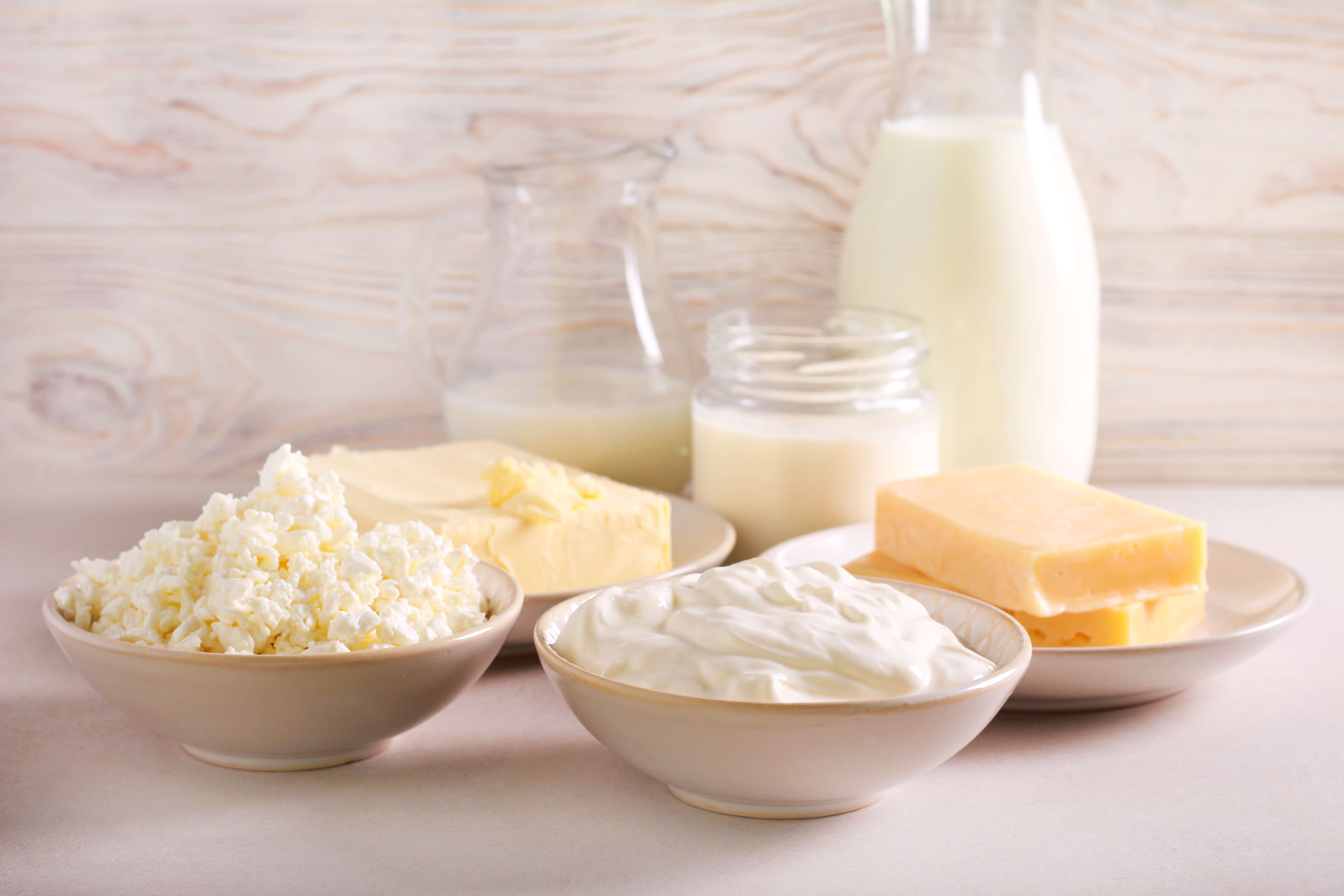
High-capacity heat exchangers have long been essential in pasteurization processes within the dairy industry. However, the frequent need to pause production for cleaning due to bacterial buildup has been a persistent issue. Any measure that extends the time between cleanings is highly valuable as it increases productivity and reduces the environmental footprint. This is precisely why Alfa Laval Extend™, a new heat-exchanger upgrade, has been highly successful at one of Scandinavia’s largest dairies.
Extend to 12-hour cleaning intervals
Alfa Laval Extend™ is easy to install and works by sending a weak, safe electrical current into the heat exchanger, which results in a bacterial reduction of 90–99% and prevents buildup. This allows the critical cleaning interval to be safely extended to 12 hours, compared to the current industry standard of 8 hours. “At the large dairy that first implemented Alfa Laval Extend™, we’ve had 30% fewer cleaning instances, resulting in a 50% increase in uptime”, says Anna Andrys, Strategic Project Manager at Alfa Laval. “Besides the productivity benefits, there are also significant environmental advantages.”
More sustainable use of resources
The dairy operates two pasteurization lines, with a total capacity of 140,000 liters per hour. With Alfa Laval Extend™, the dairy saves 7,000 m3 of water, 100,000 kWh for pumping and heating, and 35 tonnes of cleaning chemicals annually. Additionally, there is a substantial reduction in wastewater that requires processing.

“We have closely monitored every aspect of the installation together and eagerly awaited the real-life results. It’s undoubtedly a shared success.”
Anna Andrys
Strategic Project Manager Alfa Laval
A successful collaboration
When Alfa Laval contacted the dairy producer, they were eager to try the Extend™ solution. “Their contribution to this process has been crucial,” says Andrys. “Although the technology behind Extend™ is brilliantly simple and the units are easy to install, we are pioneering a new solution, and years of development and testing has gone into it.”
Making dairies greener and more productive
The Extend™ team at Alfa Laval now looks forward to introducing this biofilm-reducing technology to more dairies and new markets. “The environmental aspect is a fantastic motivation for us,” Andrys explains. “The incredible amounts of water, energy, and chemicals that can potentially be saved with a successful rollout are impressive. Of course, the substantial increase in uptime and productivity for dairies is also a great driver. The technology is easy to install and does not require Alfa Laval personnel; in-house engineers can handle the installation themselves. It can even be installed on non-Alfa Laval heat exchangers, making Alfa Laval Extend™ a true game changer.”
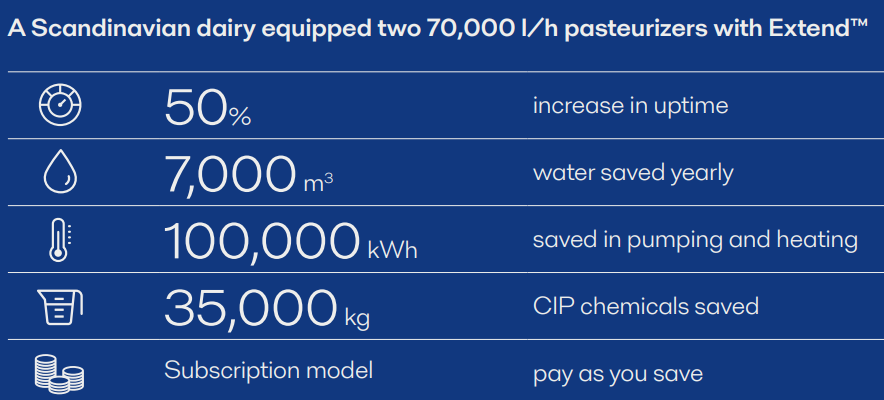
Highlighted Technologies
Benefits
• Increased uptime
• Water saving
• Energy saving
• Less cleaning chemicals
• Less wastewater